- Marketleader in no-man-entry robots
- Game-changing cleaning method
- ATEX zone 0 certified robots
Industrial cleaning robots for the food & food processing industry
Food & Food processing industry

The food industry is a complex, global collective of diverse businesses that supplies most of the food consumed by the world's population. The term food industries covers a series of industrial activities directed at the processing, conversion, preparation, preservation and packaging of foodstuffs.
Food processing is the transformation of agricultural products into food, or of one form of food into other forms. Food processing includes many forms of processing foods, from grinding grain to make raw flour to home cooking to complex industrial methods used to make convenience foods.
Robots for food & food processing industry
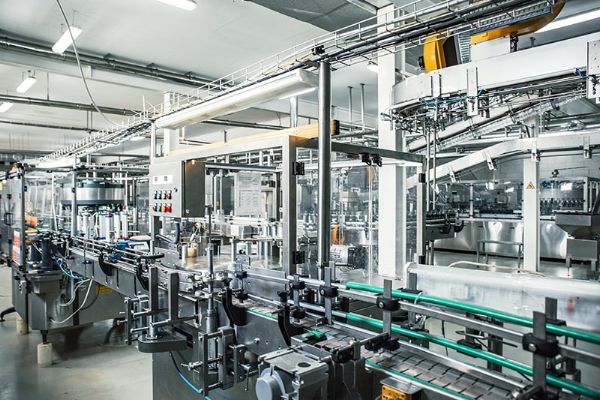
What are the risks in the food industry in terms of cleaning?
Several risks can occur in the food industry whilst performing a cleaning job. The obvious risk of the confined spaces where ventilation is limited, or working inside the factory underneath conveyor belts. Another risk which might not be the first to come to mind, is the risk of an explosive environment.
This particular risk is also known as dust explosive risk, referring to the ATEX directive as ATEX zone 20/21/22. This is found in the food & food processing industries because of particles that stay airborne and thus can create a dust explosion. Examples of these explosive risk environments in the food & food processing industry can be found in the factories where they work with sugar, flour, milk powder, cacao, tea, grains, herbs, and also additives.

Where does the cleaning happen?
The cleaning happens in and around the process but also in the storage containments before it is either transported or processed. In case of the latter, when changing of product is required, this will need to be clean to avoid a chemical reaction.
In terms of the process itself, in the majority of the factories, there are conveyor belts. To prevent the entire process from being stopped for the reoccurring cleaning, this can be done by a robot that sucks up the spillage underneath the conveyor belts. This form of online cleaning will then not limit the production as this can continue whilst the operator is out of the line of fire.
Other areas such as bunkers or silos where the product is stored can also be cleaned without the intensive labour and avoid operators going into these hazardous locations by utilizing one of the robotic solutions of KOKS Robotics.

Applications
- Robot used to clean underneath online conveyors so there is no human entry needed and factory remains open.
- Robot to clean silos in which there is a hazardous environment due to the risk of an explosive environment.
- Cleaning out confined spaces with a limited ventilation possibility.
KOKS Robotics, formerly known as ADROC Tech s.r.o., is market leader and manufacturer of innovative no-man-entry tank cleaning robotics for ATEX zone 0. KOKS Robotics is part of the Dutch company KOKS Group an international manufacturer and supplier of vacuum trucks and heavy industrial cleaning equipment, built in accordance with the latest PED, ADR (Ceoc), DOT 407/412 standards. Founded in 1989 and has since grown into a dynamic company that operates globally and consists of eight specialised subsidiaries in the USA, The Netherlands, the Czech Republic, Saudi Arabia, Slovakia and participations in rental organizations that operate in the Netherlands and the United Kingdom. As a growing, innovative, healthy and reliable company, KOKS Group has gained an excellent reputation in the (petro)chemical sector and other industries as a vacuum truck builder.
